Core Production Capabilities
07/24/19
Our broad production technology and expertise is based on years of manufacturing experience that provides a platform for the manufacturing of products that meet the highest standards.
Sterile Filtration, Aseptic Processing and Filling
Sterility is a key product attribute for our products. All of our sterilized products are processed in a cleanroom under laminar air flow hoods. A variety of sterile filtration schemes are utilized. Personnel gowning and cleaning room practices are implemented to control and minimize contamination. Aseptic techniques, sterilization of components and stringent practices are followed to ensure products are free of contamination and meet sterility requirements.
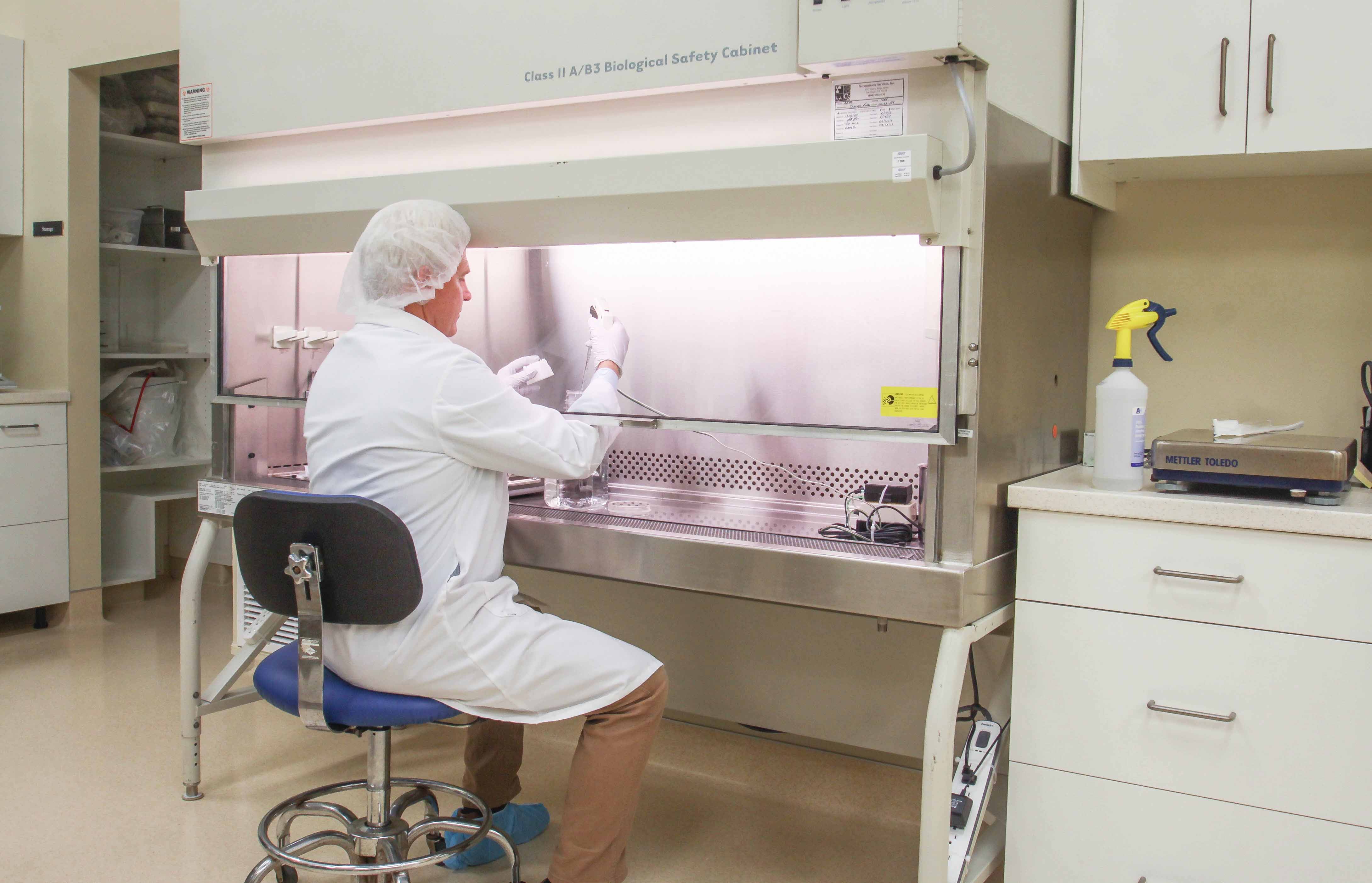
Ultra and Dia-Filtration
Various ultra and diafiltration techniques are utilized to both concentrate materials and remove low molecular weight materials. The UF/DF production scale ranges from less than a liter to thousands of liters with a range of molecular weight cutoffs being employed. These techniques allow for products to be of higher purity and achieve desired concentrations of products.
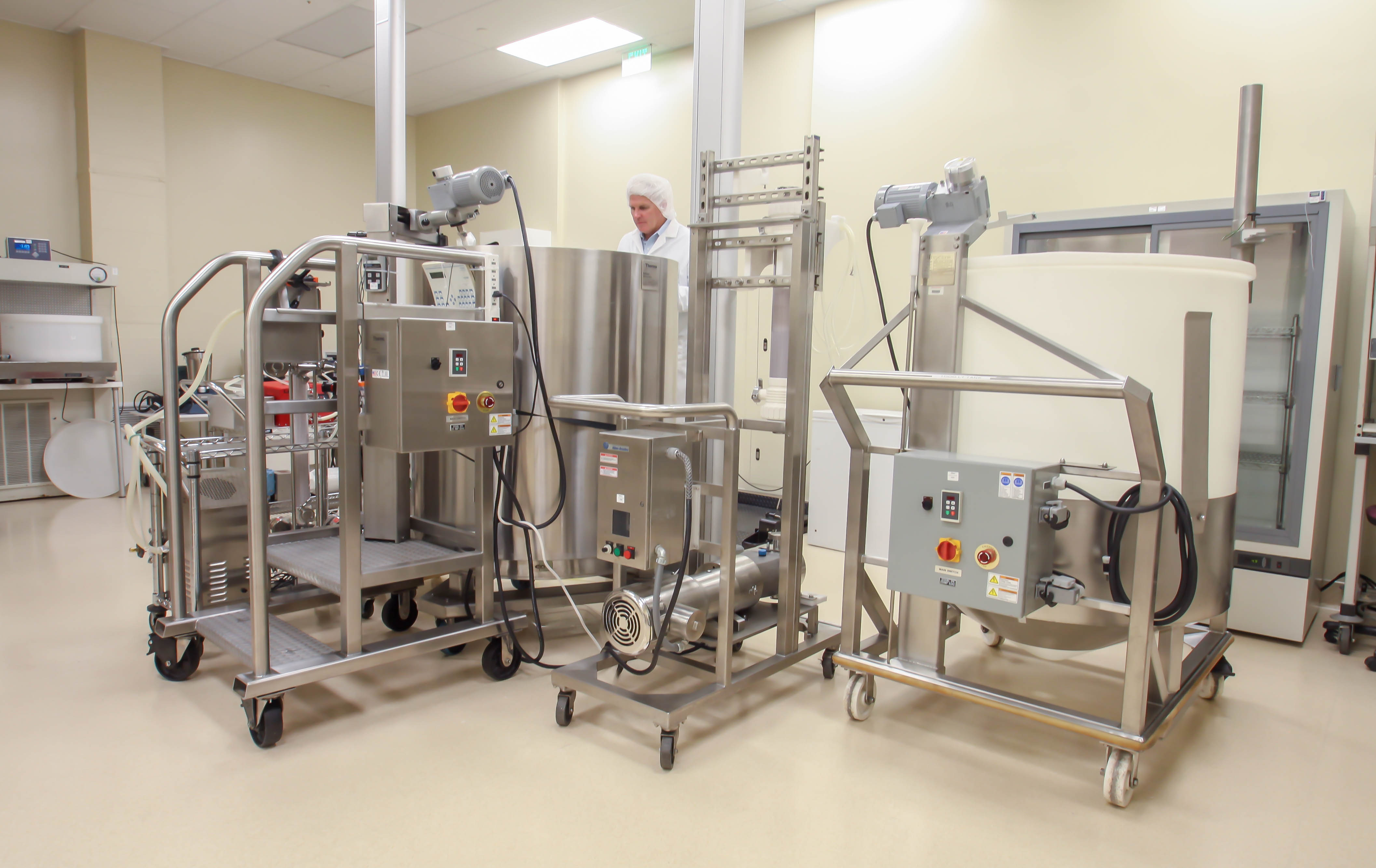
Autoclaving, Irradiation and Ozone
A variety of process methods are used to sterilize products and components. The processing parameter for each of these sterilizing methods have been precisely determined and controlled. Dosages, exposure time and temperature levels along with penetration and packaging parameters have all been set so as to ensure sterility of products and components.

Blending and Homogenization
Many of our manufacturing processes require the blending and homogenization of viscous solutions and mixtures. A variety of mixing techniques have been developed to uniformly homogenize mixtures with various buffers and ingredients. Control of mixture temperature, pH, salt content, mixing times and speeds are important parameters to control to ensure proper and homogeneous mixing of materials and products.
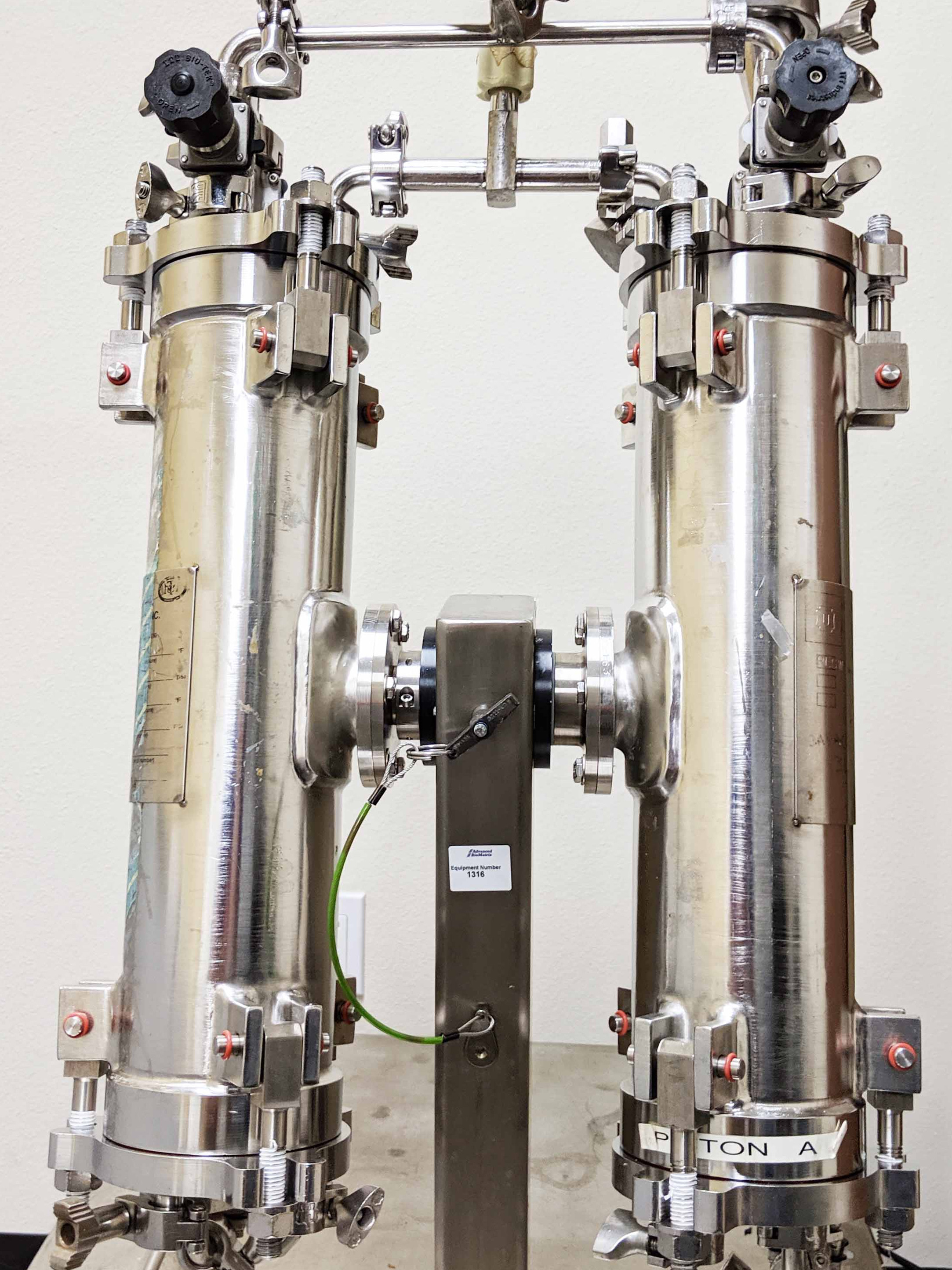
Particle Size Reduction and Grinding
Some processes and products require that materials have certain uniform particle size. Several production methods are used to grind or reduce the particle size of material to meet the requirements, such as grinders or through sonication. Consistent particle size is important in solubilization and enzymatic treatment of materials. Processing parameters such as grinding time, temperature, particle size and sieve size are set to meeting manufacturing and product requirements.
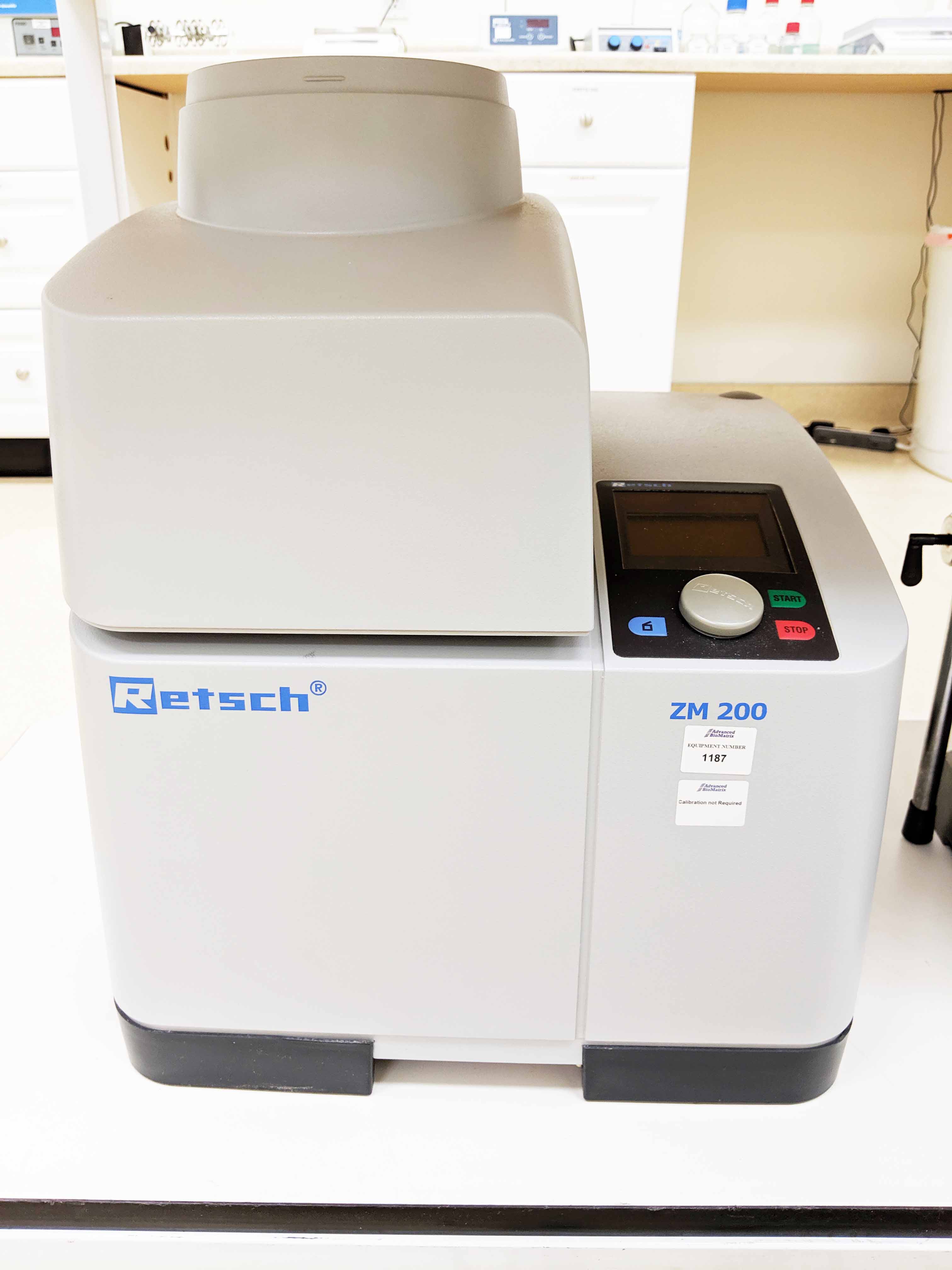
Protein Isolation and Purification
A number of purification methods have been developed to purify products. These methods include ion exchange, filtration, extraction, ultrafiltration, pH, size exclusion, precipitation, centrifugation and diafiltration. Each of these protein and product isolation and purification methods follows defined processing steps under controlled parameters.
Filtration, Clarification and Ion Exchange
Specialized filtration and clarification techniques are used throughout manufacturing processes. These methods remove certain unwanted materials or contaminates via filtration or chemical and ionic adhesion. These processing methods play an important role to ensure that products are of the highest purity.
Lyophilization
Lyophilization (freeze drying) is an important process for many products to better preserve and stabilize the material while elongating the shelf-life. Detailed recipes have been set to control the temperature and vacuum levels over the processing time for optimally drying a variety of materials. Techniques have been developed and implemented to maintain the sterility of the product throughout the lyophilization cycle. Bulk lyophilization and vial lyophilization cycles have been set up accommodating both large and small volumes of materials.
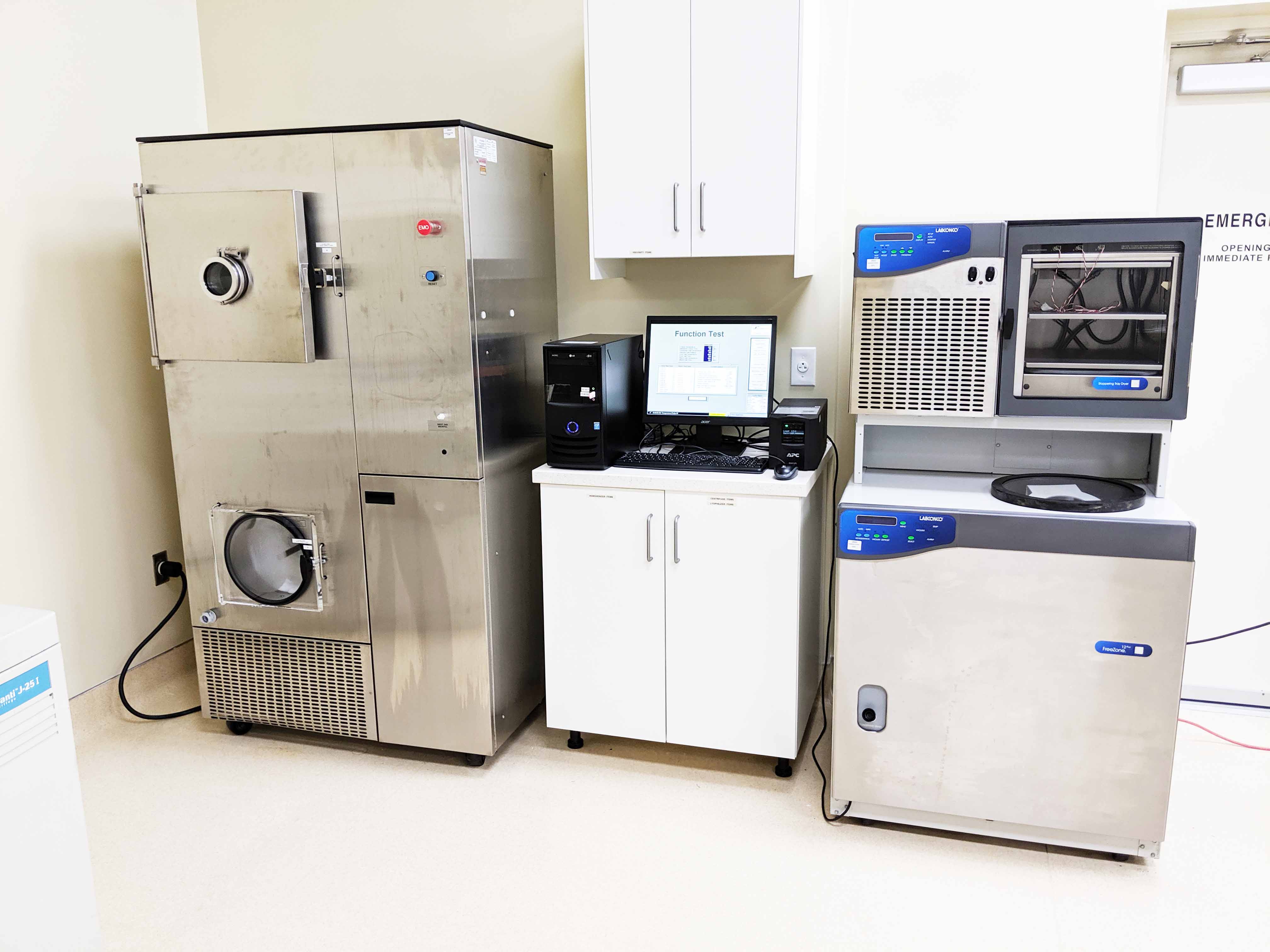
3D Bioprinting
With the introduction of natural bioinks, 3D bioprinting is a key method for the development and testing of various bioink formulations and products. We have several bioprinters that are used to demonstrate the attributes and characteristics of our bioink products. In conjunction with bioinks, we utilize a bioprinting support material to maintain the structure and resolution of the 3D printed structures throughout the printing process. Virtually any structure, or tissue can be extrusion printed with our unique bioinks with high fidelity and resolution.
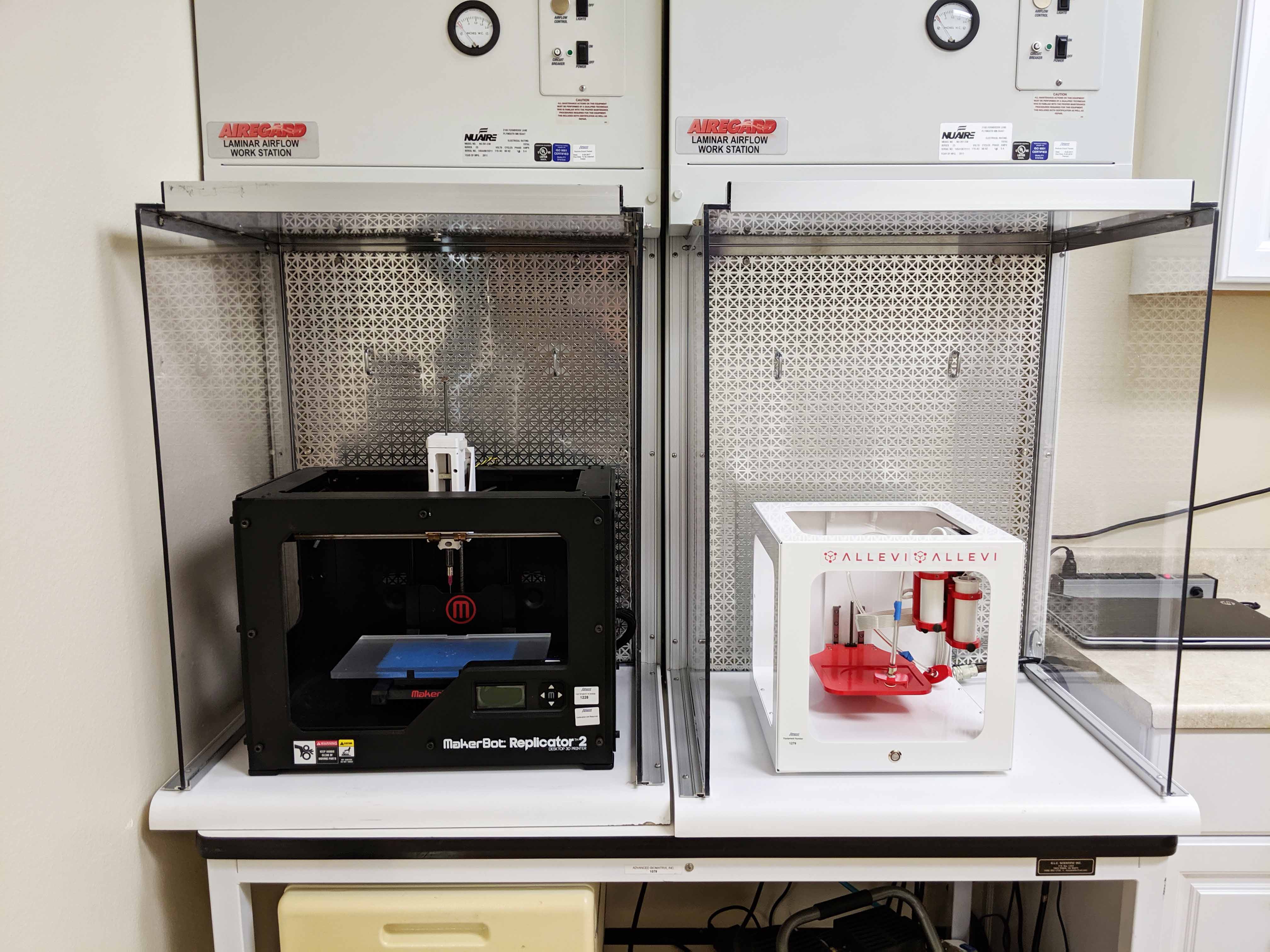
Crosslinking (Photo, Chemical, Thermal)
To enable the tunability of hydrogels, a number of crosslinking methods have been developed. For photo-crosslinking, several photo initiators have been selected that can crosslink hydrogels using various wavelengths of light. Additionally, chemical and thermal crosslinking methods have been incorporated into our products to provide a broad range of either tunable, or more robust biomaterial for our customers.
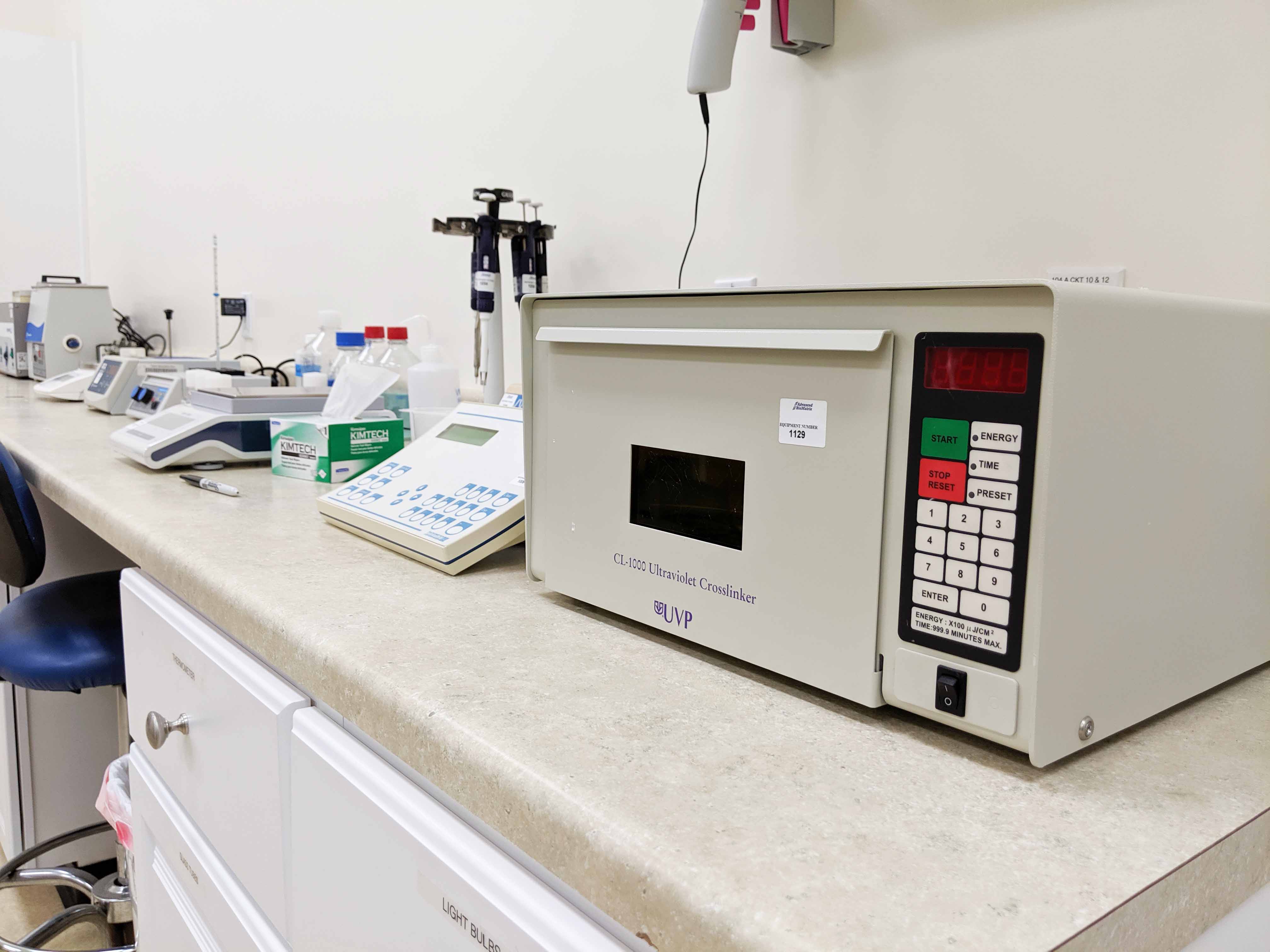